Functional and protective coatings
VNIINM has been the leading organization in developing nuclear technologies and materials for the Russian nuclear industry for several decades. High complexity and non-standard setting of objectives, increased demands on the results of developments which VNIINM deals with resulted in the accumulation of unique competencies in the scope of functional and protective coatings.
Currently, VNIINM is one of the leaders, both in Russia and globally, in the field of technology for applying protective and functional coatings having a wide range of applications, with the use of various technological processes that allow us to produce a new generation of products with a radically improved price/quality ratio.
A project to create a modern industrial production of functional nanostructured coatings based on advanced innovative developments of VNIINM is under consideration. This production has no analogues in Russia and uses a wide range of coatings, technologies, and application equipment. The new technological complex will be one of the bases of the revival of domestic machine building, it would serve to improve the efficiency, reliability and expand operational capabilities of engineering products used in the fuel and energy sector, mechanical engineering, petrochemical and mining industries, aviation and power turbine construction, etc.
The use of innovative developments in the field of coating application would cause the following effect:
products would have unique properties (new quality), which cannot be achieved without coating.
the quality would be improved, and service life of products increased.
cost of products would be reduced.
Import substitution.
The latter aspect is very important. The Russian market is undersaturated with equipment required to produce reliable coatings. Coating technologies have always been dual-use technologies, thus their export to USSR and Russia was restricted for a long time. Domestic enterprises have mastered the production of simple equipment for electric arc metallization and gas-flame sputtering, but today their production is almost discontinued, while plasma and high-speed sputtering installations existing on the market have been mainly imported until recently.
Russian aviation and oil/gas coating markets enjoy the most offers of microstructured coating products. But even in these markets, the penetration of domestic coatings does not exceed 30% of similar foreign products. Domestic nanostructured coatings are not used widely on the Russian market.
Examples of potential solutions and those already implemented by VNIINM in the sphere of functional and protective coatings are:
Composite heat-resistant and refractory coatings used for protection against wear and heat of turbine parts; wear-resistant, solid-lubricant, corrosion-resistant coatings for aircraft engine parts and avionics; anti-icing coatings; replacement of electroplated chrome plating on hydraulic parts and landing gear; repair of helicopter parts; corrosion protection of fuel tanks; corrosion protection of airfield structures, etc.;
Multicomponent coatings based on heat-resistant alloys with high corrosion and wear-resistant properties to increase the service life, heat resistance and thermal stability of the valve-piston system of internal combustion engine, fuel equipment of diesel engines, and other elements of vehicles;
Application of solid-lubricant, anti-gripping coatings on gears of heavy-duty gearboxes, on elements of sliding bearings of diesel engines of all types resulting in fuel consumption reduction, increase of power, improvement reliability and reduced noise;
Application of multilayer nanostructured coatings for equipment, products and structures of the nuclear industry;
Protective coatings for large containers in the nuclear industry, including transportation
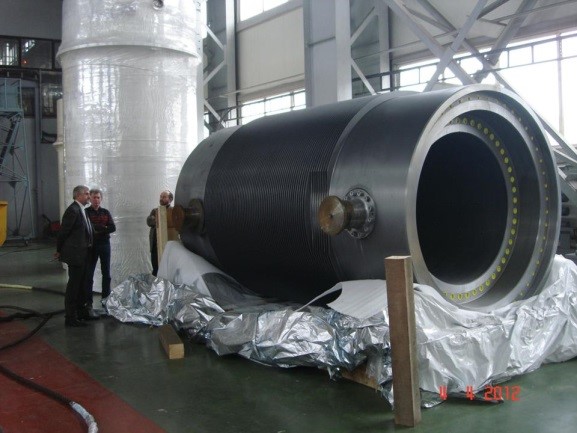
packaging systems made of high-strength cast iron with the use of spherical graphite. Previously, it was considered impossible to apply coating on these materials;
Radar-absorbing coatings for use in aviation and rocket technology, including advanced unmanned systems;
Application of multicomponent coatings based on stainless steels, aluminum-chromium alloys, etc. with high corrosion and reflective properties to replace environmentally harmful chemical and electroplating technologies used to protect against corrosion, as well as to impart ornamental properties to products;
Application of thin ceramic coatings on metal and non-metal (including composite materials, plastic, rubber, glass, etc.) products and parts to radically improve properties of products in terms of heat resistance, wear resistance, and resistance to aggressive environments;
Operational repair and restoration of housing and communal water supply systems by applying metal coatings on-site using mobile (in particular, portable) installations. Anti-corrosion protection of pipes, fittings and equipment with a lifetime warranty.
Operational repair of machinery, equipment, metal structures, and pipelines using mobile (portable) coating installations.
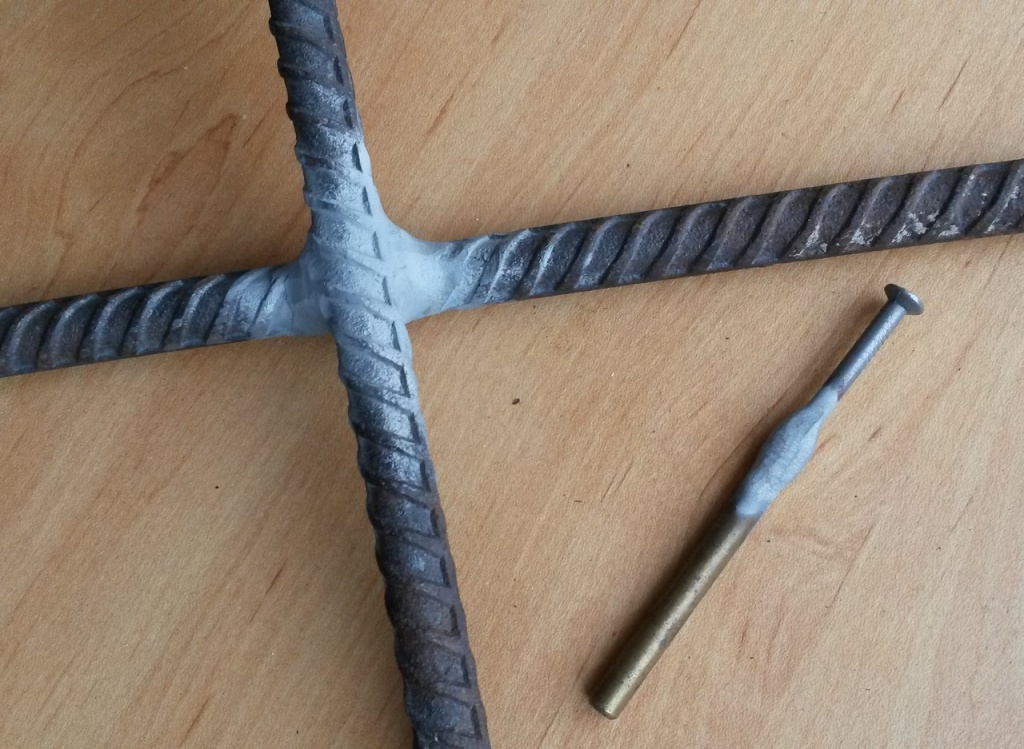
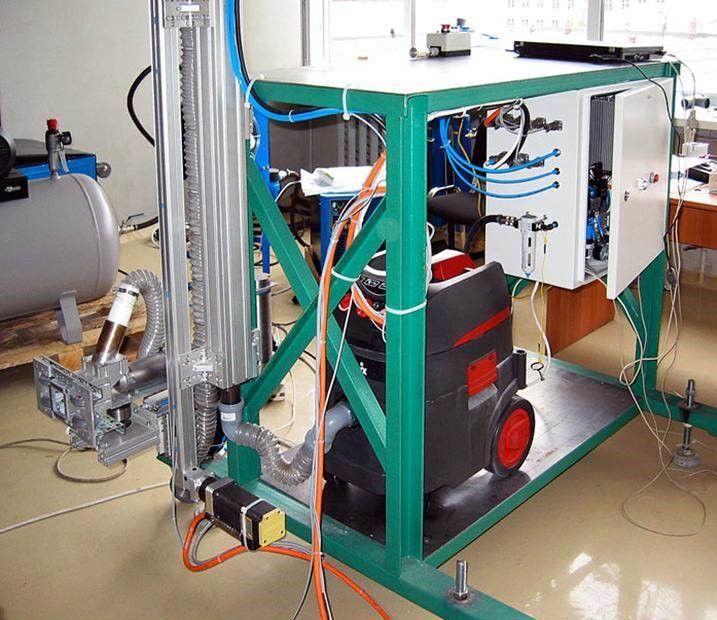
Development and manufacture of industrial robotic coating systems. The complexes have a high degree of automation, which provides flexibility in setting modes of application of complex multicomponent coatings on products of various shapes and sizes.